A standard set of design guidelines exist to determine the proper ORing dimensions for radial and axial seals of a given dimension Technical sealing has been defined by DIN Standards as follows Static Seal The sealing action created between two mating surfaces with no leakage of liquid or minimal diffusion of gasOrings are the epitome of elegant engineering The ring itself costs only a few cents, and the groove it goes in is simple and easy to manufacture But despGeneral Engineering Menu ORings Suppliers Molded ORings Services ORings Design Guidelines, Specifications, Materials An Oring , also known as a packing , is a flexible gasket in the shape of a loop;

O Ring Groove Design Seal Design Inc
O-ring shaft seal design
O-ring shaft seal design-In most static applications, a Square Ring will serve as a direct replacement for an oring and generally will perform a highpressure sealing function as well as or better than an oring For more information or to request a quote on Square Rings, please give us a call at or submit the Product Inquiry FormThe chamfers facilitate assembly and protect the Oring from damage during the installation process The Oring and all surrounding parts should be well lubricated before assembly, preferably with the same fluid as used in the hydraulic system, ensuring compatibility with seals and cylinder components Extrusion gaps and backup rings
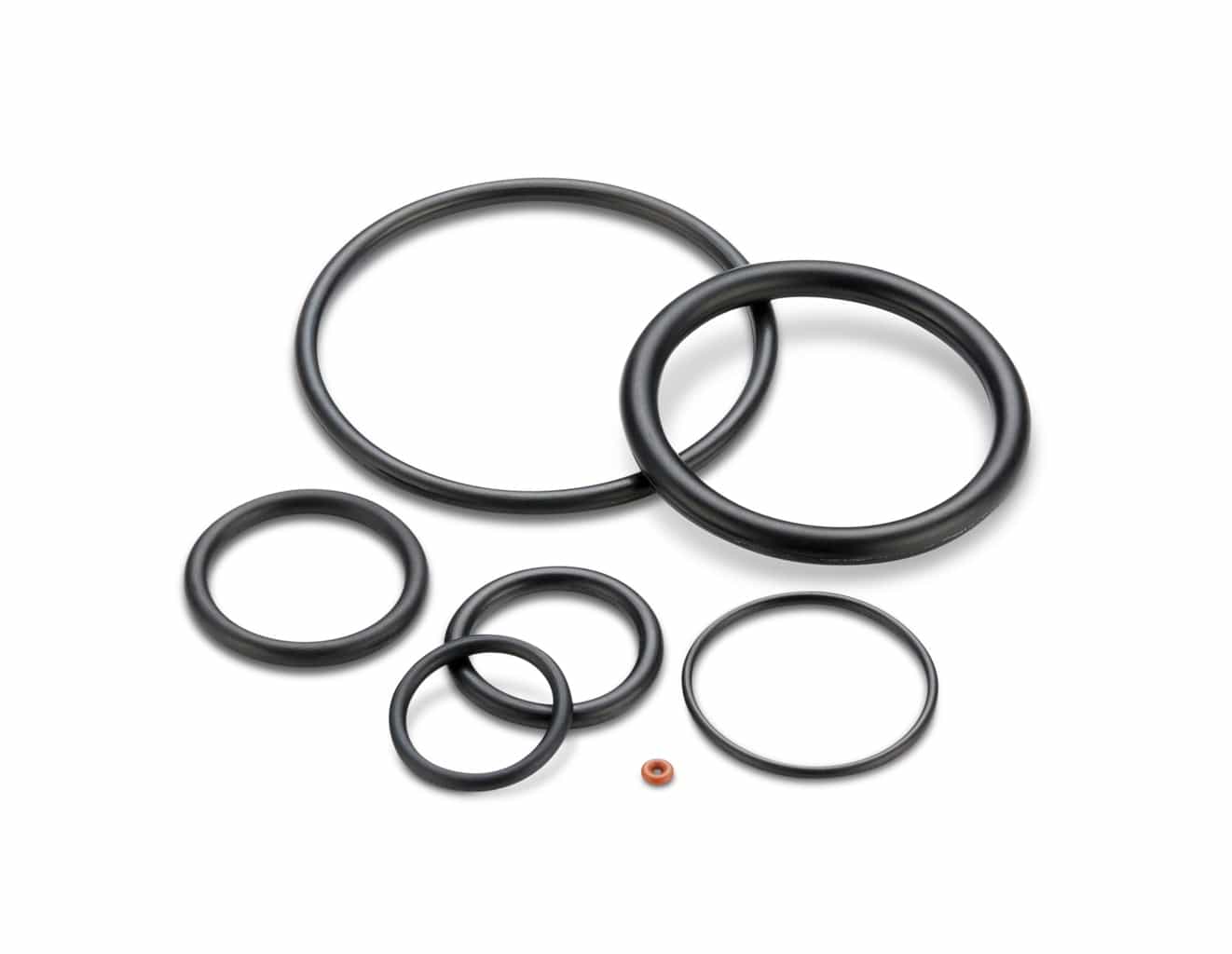



Groove Design O Ring Seals Minnesota Rubber Plastics
Rubber Seals, Sealing Devices & ORing Seal Design AppleOring groove design guides offer default dimensional guidance on the most basic oring groove design applications The best orings are useless without the right groove design which becomes increasingly important the more demanding the application environment XRing Seals and high performance ORing material groove design follows the sameAn Oring is a torus, or doughnutshaped ring, generally molded from an elastomer, although Orings are also made from PTFE and other thermoplastic materials Orings are used primarily for sealing Orings are designed to be seated in a groove and compressed during assembly between two or more parts, creating a seal at the interface
ERIKS standard ORings and load them also into your created design info chemical volume swell (%) cross section diameter (mm) ISO 3601 free Calculate Results Reset calculatorGroove design guide for static oring face seals provides default recommendations on width, depth, diameter and more for basic applications Oring face seals are used in a variety of applications, including bolted flanges or removable lids Simple selection tool toOne general guideline for good Oring application and design is to maintain a range of % sqeeze on the Oring (~1040% for static and no more than 30% for dynamic) No less than 75% of the seal crosssection should be contained within the groove to ensure the seal does not "roll" or extrude out of the groove
Lepu m3n o ring seal design for wholesale for oil SGS,ISO,CE/UL/SGS/ M7N mechanical seal made by lepu seal is a popular seal replacement for eagleburgmann m7n this seal we made is a Self cleaning effect seal, and insensitive to low solids contents, this seal design offer strong flexibility in torque transmissions, and for this seal, LepuDynamic Rotary ORing Gland Design In a dynamic rotary seal applications a turning shaft protrudes through the ID of an oring, the oring then becoming a seal The table below lists recommended dimensions for dynamic rotary seal glands by AS568A oring dash numbers Static Radial Glands Axial Internal PressureAn Oring has proved to be a practical rotary shaft seal in many applications With the correct design, Parker ORing rotary seal compound N, will provide satisfactory service at surface speeds up to 1500 feet per minute The design conditions are most critical for rotary seals, as would be expected
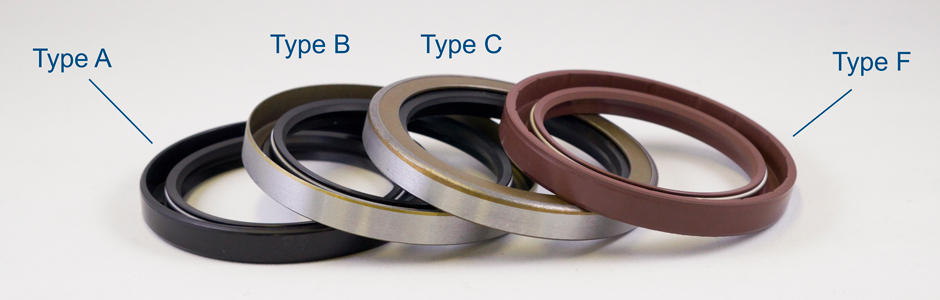



Oil Seals Lip Seals Rotary Shaft Seals Buy Online Polymax Uk




Oil Seals Radial Oil Seals Trelleborg
Designing the parts of an application where orings will be applied is broadly termed "oring groove design" In order to seal properly, the oring has to deform in the application by being compressed and stretched in any number of ways The design of the groove where the oring sits plays a major role in how the oring performs its sealing The Parker ORing Handbook is a hardcover manual with 11 chapters detailing Oring design The chapters range from tutorial to purely technical in nature For instance, technical chapters provideCal drive belts More information, including design criteria on Oring drive belts and their application will be found in ORing Applications, Section III 12 What is an ORing Seal?



Widely Used Different Type Oil Resistance Seal Tractor Rubber Shaft Oil Seal In Competitive Price Buy Rubber Shaft Seal Tractor Oil Seal Oil Resistance Seal Product On Alibaba Com
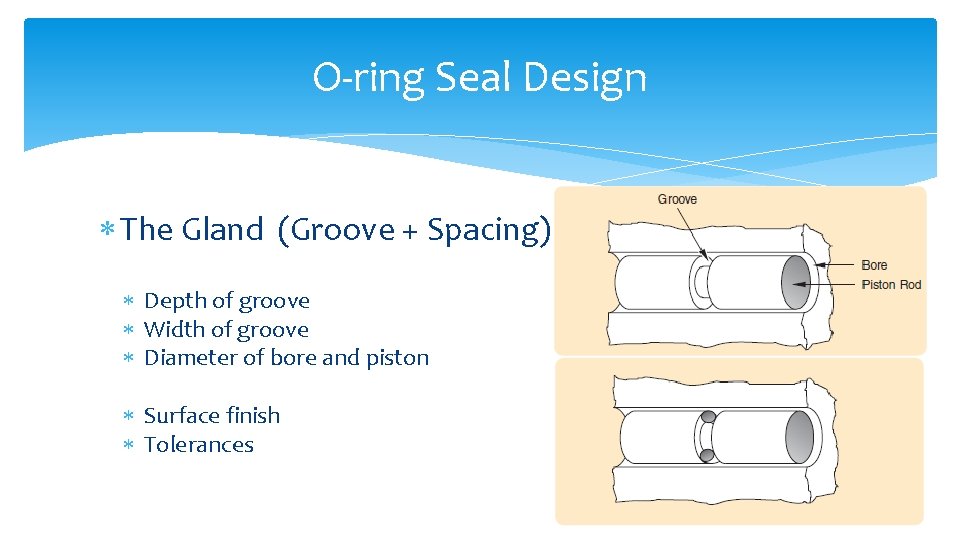



Design Of Oring Seals Design Of Oring Seals
'O' Ring Guide Introduction The 'O' ring, or toroidal seal, is an exceptionally versatile sealing device Applications, ranging from garden hose couplings to aerospace or oil and gas duties, make it the world's most popular volumeproduced seal 'O' rings offer many benefits to designers, engineers, maintenance staff and plantIt is a elastomer with a round crosssection designed to be seated in a groove and compressed during assembly between two or more parts, creating a seal at the interfaceReciprocating seals are a dynamic version of either a male radial or female radial Oring design In a reciprocating seal, there is relative reciprocating motion (along the shaft axis) between the inner and outer elements This motion tends to slide or roll the Oring, or sealing surface of the Oring, back and forth with the reciprocal motion
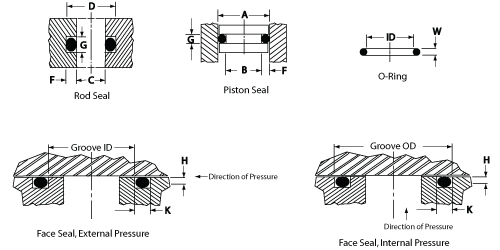



O Ring Groove Design Daemar Inc



1
If you are designing a face seal, select the ORing with an inside diameter which will position the ORing on the side of the groove opposite the pressure Click here for more information on face seal groove design Note the ORing inside diameter for the next step Calculate the Seal Stretch Using Equation 1, calculate the installed seal stretchRotary ORing Limitations Oring seals are NOT recommended for rotary applications under the following conditions Pressures exceeding 900 psi Temperatures lower than 40° F or higher than 225° F Surface speeds exceeding 600 feet per minute (fpm) 2300 rpm for 1 inch diameter shaft 1150 rpm for 2 inch diameter shaft8 Select the Seal Select the proper QuadRing® Brand size from the Standard Size tableStart by turning to the section of the table for the crosssection size you have selected, and then finding the QuadRing® Brand for the proper size bore or rod (shaft) you are sealing
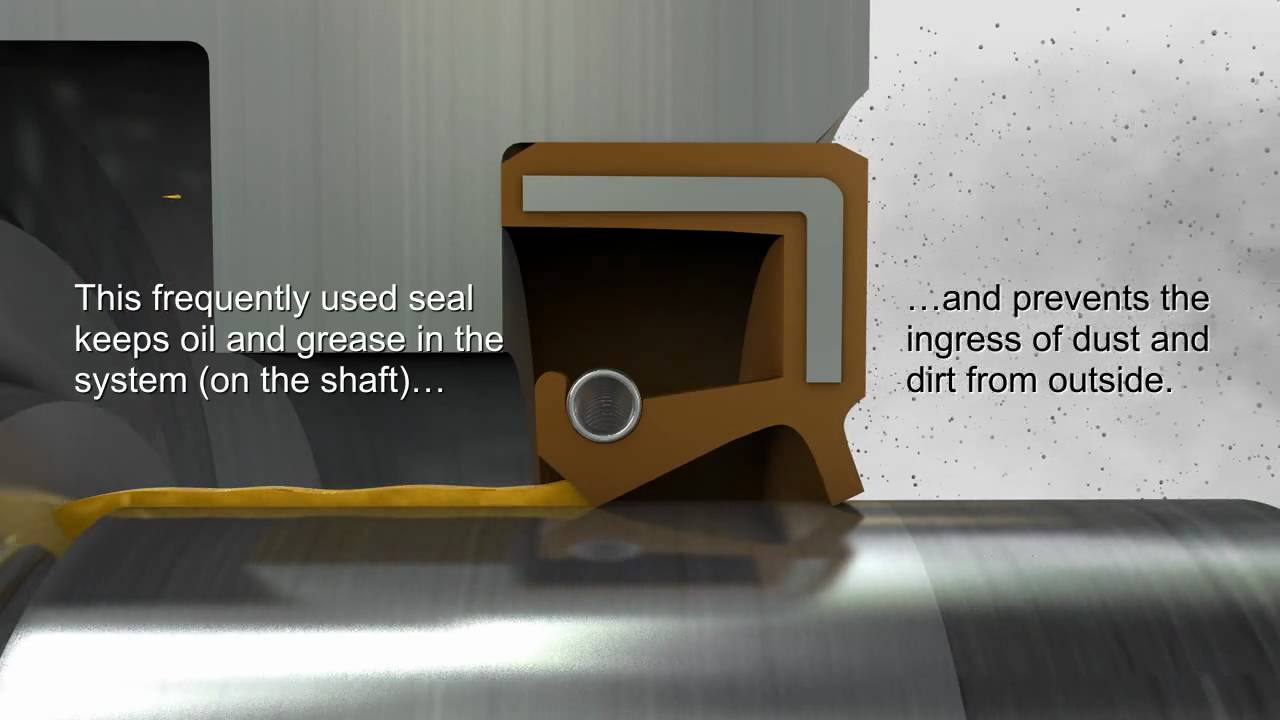



Shaft Seals Trelleborg Sealing Solutions Youtube




Customized Customized Rubber X Ring Seal Manufacturers Suppliers Factory Direct Wholesale Xlong
Dynamic Oring Shaft Seal Dynamic oring shaft seals are typically utilized in rough vacuum pressure regimes for transfer of rotary motion by means of a solid shaft through the vacuum environment Two dynamic oring seals are present against the solid shaft These units are typically used with speeds 100rpm and for cost sensitive applicationsDescribes the function of an Oring IN THE GROOVE An Oring seal has two essential parts the Oring and the glandThe gland consists of the machined groove into which the Oring is installed andthe mating surface to be sealed The primary components of rod and piston glands are shown in Figure 1 A seal is effected when an Oring is squeezedOrings and backup rings maintain sealing contact force by radial or axial deformation in the seal housing between two machine components The most important criteria that influence the maximum operating pressure at which Orings in static radial sealing can be used



Www Fluorotec Com Media 2191 Aft Seals Design Handbook Pdf




Single Seals For Caustic Environment In Pumps
Be it dynamic or static operation, radial or axial loading, vacuum or high pressure Rubber lip seals (figure 2), provide a very compact and simple solution to sealing rotating shafts However, their use is restricted to low pressure applications, (less than 01MPa) and moderate temperatures, up to 150°C Figure 2 Rubber lip seals For higher temperatures and pressures, mechanical seals based on sliding contact between theTo find the groove dimensions on a rotating seal, use Design Chart 5 Find the shaft size in the second column The groove root diameter and width will be found under their respective columns The Pressure Seals Oring size will be found in the first column next to the shaft diameter BACKUP RINGS (Design Chart 7)
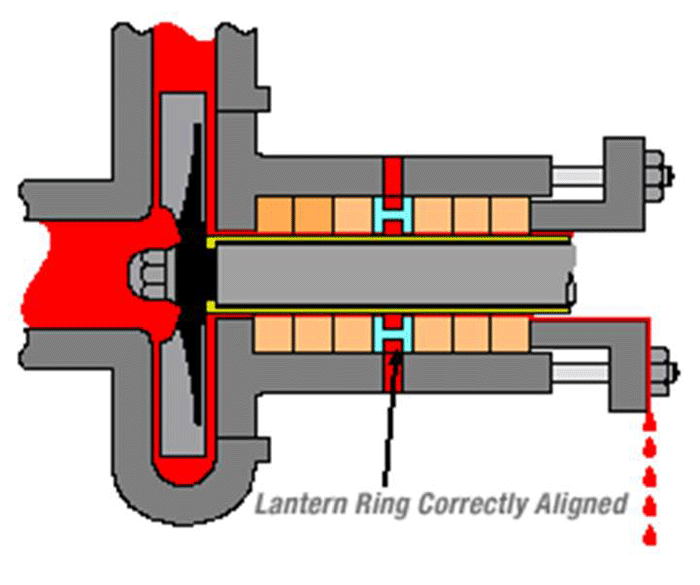



Shaft Seals For Rotating Shafts




O Ring Groove Design Seal Design Inc
The greatest number of dynamic seals are used in reciprocating service in cylinders, valves, and linear actuators Oscillating motion is encountered in swivels and valve stems When an ORing is used on a rotating shaft, it should be limited to light duty where the shaft speed is low and some fluid bypass is acceptableEnhance your sealing efficacy with indestructible o ring shaft seals available at Alibabacom These o ring shaft seals are innovatively designed for excellent performance and safety and create miracles Help the customers to design and improve the products F Add to Favorites 1/6 YSRUBBER rotary shaft seal o ring 40mpa $001$030 Seal Daemar's extensive line up of sealing products has been developed to provide exceptional value by combining the quality and performance that design engineers require with the total cost of ownership savings that today's businesses demand




Diagram Of The Face Seal Design 1 Seal Ring Flexibly Attached 2 Seal Download Scientific Diagram
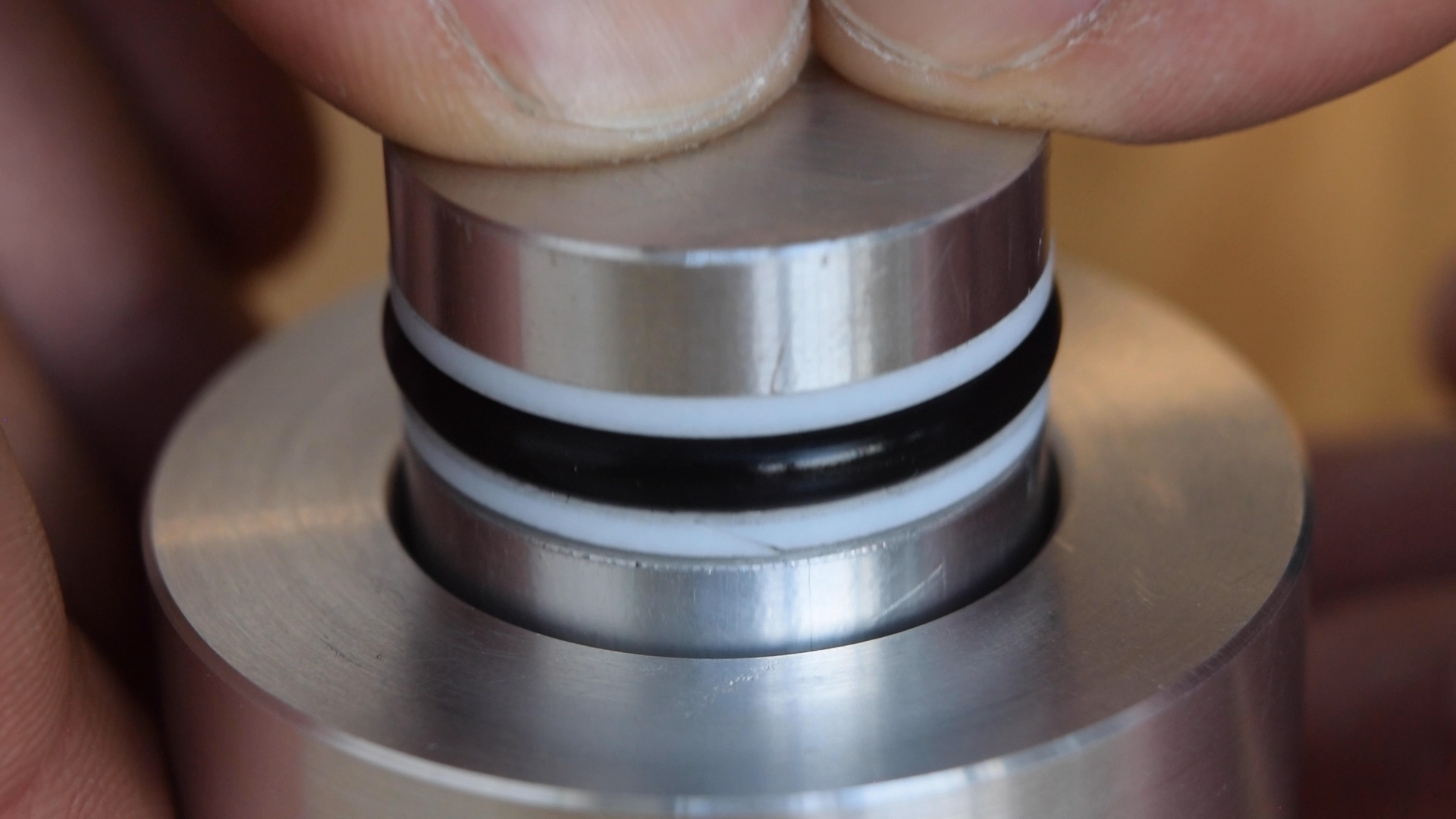



O Rings O Yeah How To Select Design And Install O Ring Seals Tarkka
An Oring seal is used to prevent the loss of a fl uid or gas The seal assembly consists of an elastomer O12 Oring Gland Design The following pages contain basic Oring gland design information Please contact the local ERIKS representative if an application does not clearly fall into these design parameters Static Applications There are five types of static Oring applications • Flange seal • Radial seal • Dovetail seal • Boss sealAn instructional video on how to assemble an oring seal on a 40K cell piston rod
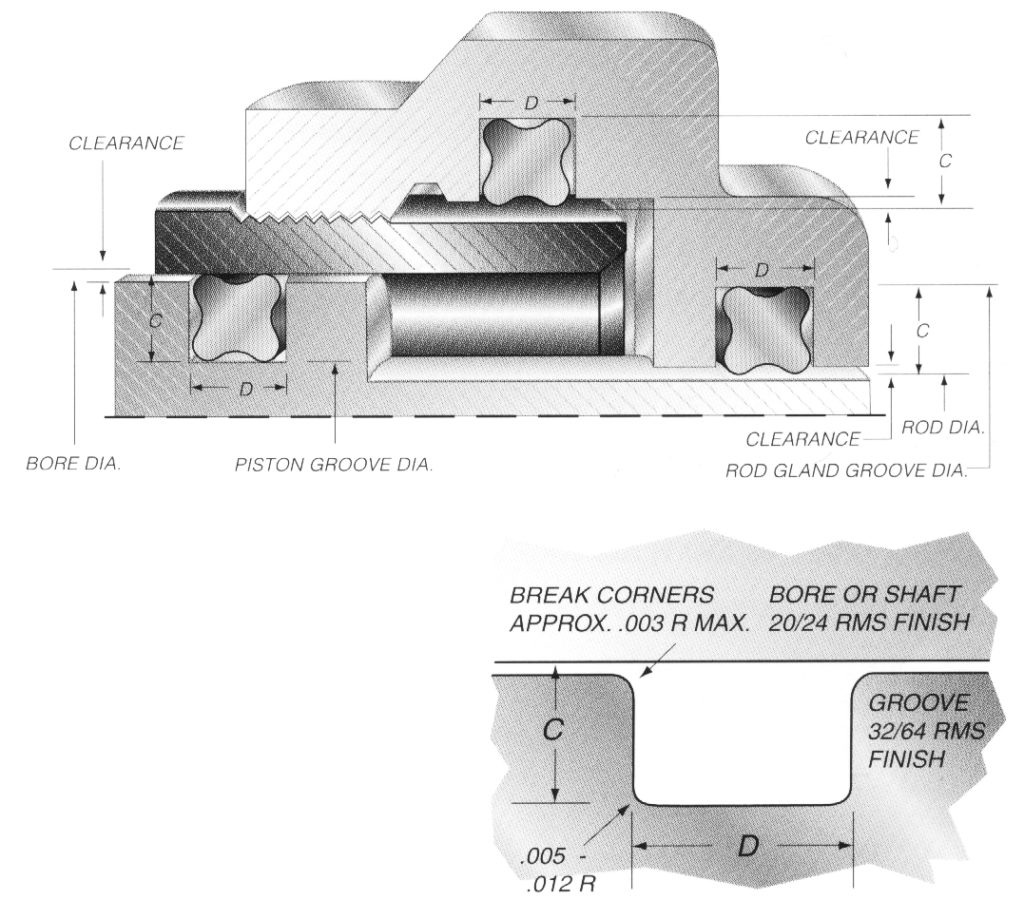



Quad Ring Groove Design Daemar Inc




What Is An O Ring Selection Material And Storage Barnwell
Some of the basic ideas of good ORing installation design are put good compression on the Oring while preventing the groove from exceeding 100% fill use a lead in chamfer in radial seal applications at an angle of 15 degrees, with an opening which exceeds the maximum height of the ORing in the grooveO'ring Groove Design As important as the o'ring seal itself is the groove that the o'ring seats into The groove must be designed to accommodate not just the o'ring size, but also its intended usage;Preliminary Oring Design Considerations An oring is a simple and versatile ring shaped packing or sealing device Having a circular cross section that functions as a seal, in both static and dynamic applications, by being compressed between the mating surfaces comprising the walls of the gland, in which it is installed



Fundamentals Of Mechanical Seals Seal Faqs



1
Oring, seal tips mechanical shaft mechanical seals pneumatic seals abrasion orings extruded rubber low temp seals oil seal materials oil seal basics FEP/PFA encapsul 1 FEP/PFA encapsul 2 neoprene oring nitrile oring lathecut oring acid orings hydraulic seals high temp seal rubber oring metric sizes Glossary of terms Face seals are actually really tricky to get right, because squeezing the Oring requires a great deal of pressure This first lid design is far too thin, and in the middle, there is virtually no squeeze on the Oring, and hence no sealing We can fix this design by adding a lip around the perimeter A third type of design is a boss sealRotary ORing Seal Glands, 552 Bar (800 psi) Max See Rotary Seal discussion in Dynamic Seals section before using this chart Note Due to effect of centrifugal force, do not locate groove in shaft Refer to Design Chart 54 (below) and Design Table 54 for dimensions Rotary ORing Seal Glands, 552 Bar (800 psi) Max (c)
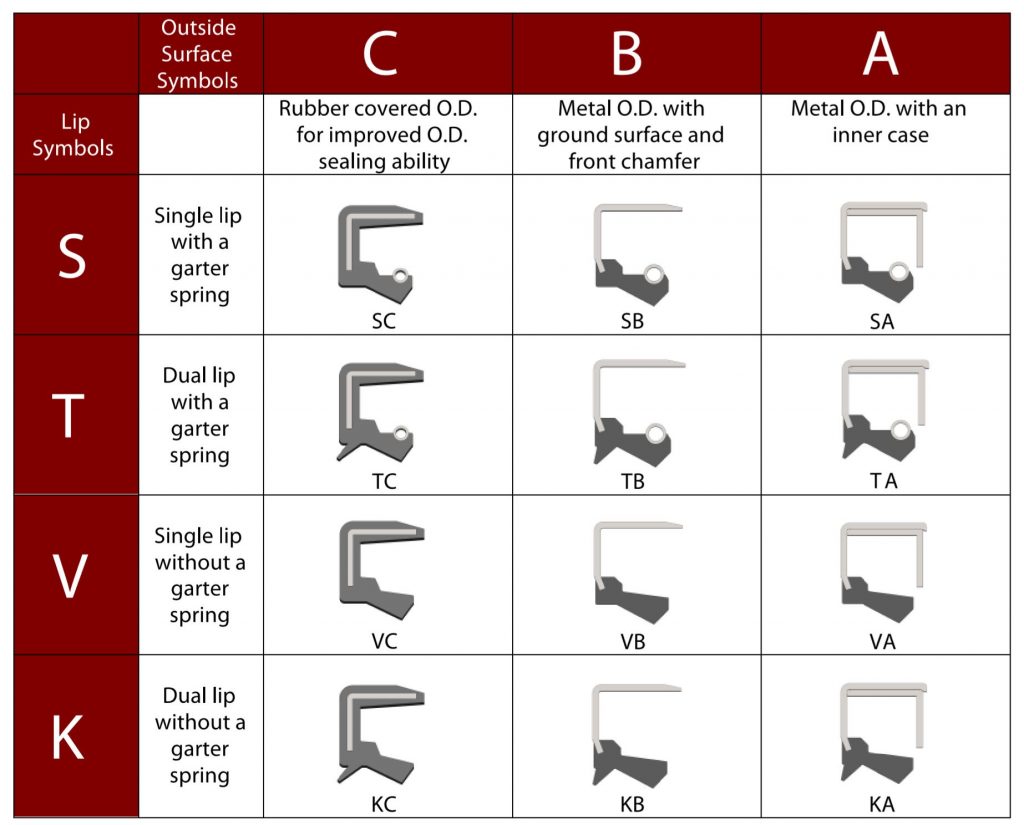



Inch And Metric Oil Seal Types Gbsa Oil Seal Manufacturers
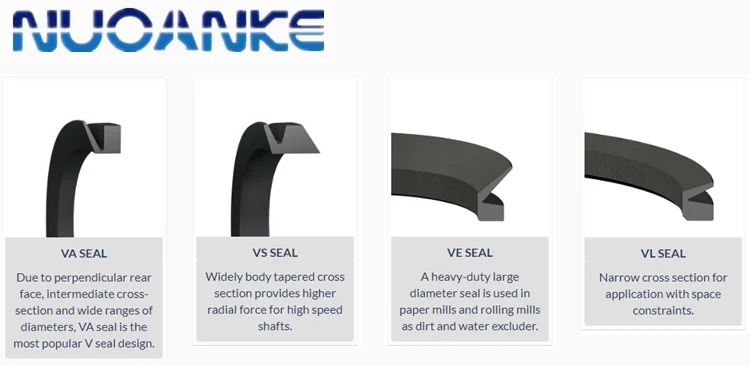



Water Seal Rubber V Seal V Ring Va Vs Vl Rotary Shaft Seal Ring Buy Rubber V Seal Vs Ring V Seal Product On Alibaba Com
Now, follow the steps below to design your own oring seal and oring groove Step 1 Choose your rubber properties by going to our Oring Material Guide section Step 2 Make sure that the material you choose will withstand the temperature of your system by going to this rubber temperature range chart Step 3Seal & Design Established in 19 by Dean T Penman, Seal & Design Inc has established itself as an industry leader in the sealing and gasketing industry Seal & Design is a leading manufacturer and distributor of die cut gaskets, seals, orings, and molded rubber products Dean's original philosophy included exceeding customer expectationsThe Groove Width GW should therefore be about 15 times the ORing crosssection diameter to accomodate this axial expansion, Design Guidelines for Axial Seals ORing design for axial seals is similar to that for radial seals, with the important points summarized below The ORing must be compressed by a predetermined amount, and this
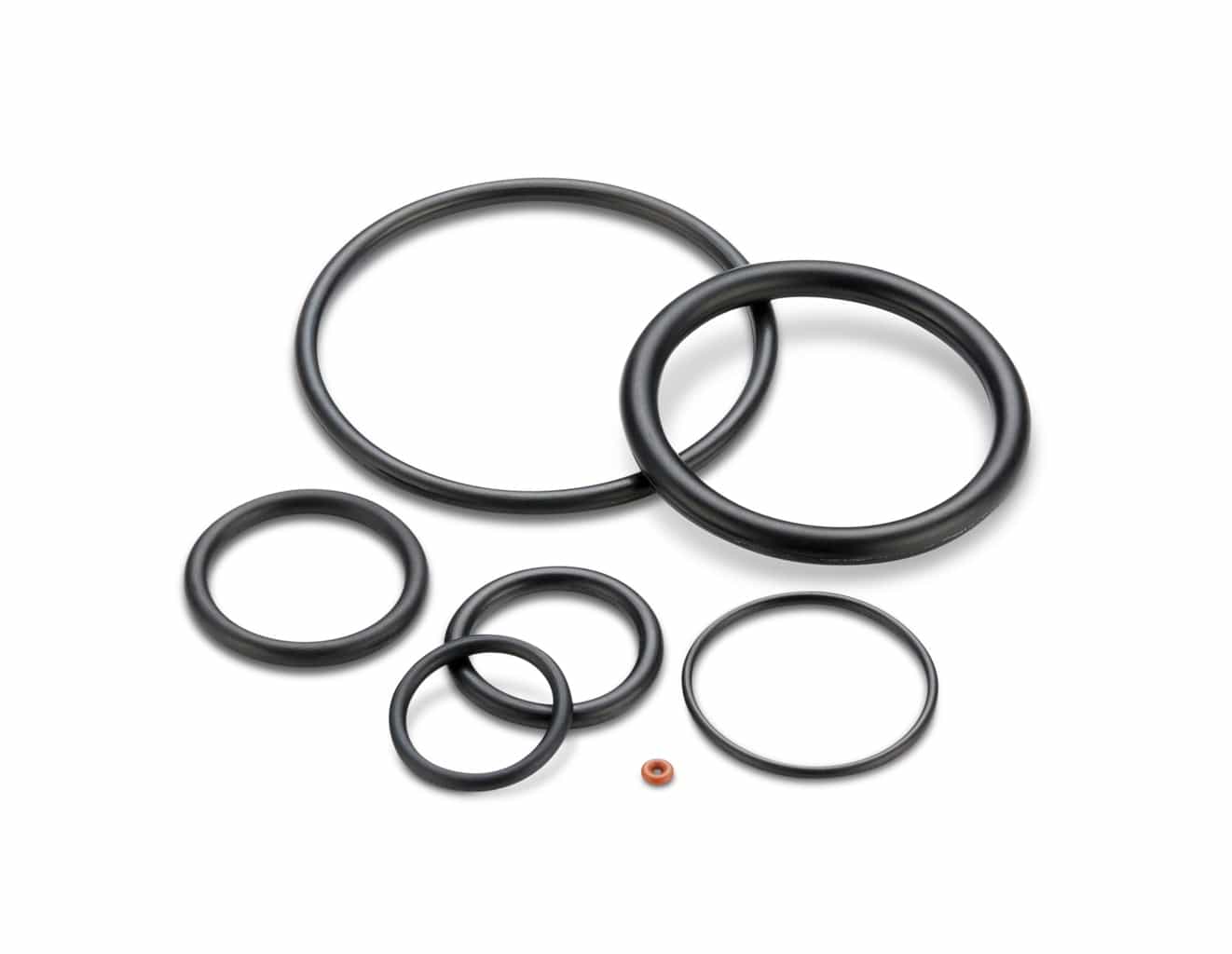



Groove Design O Ring Seals Minnesota Rubber Plastics




Fundamental Of O Ring
Sed circulation around the seal faces The machined, recessed Oring groove helps prevent the seal from clogging due to build up of product around the shaft Oring Seal drive is provided by the conical spring tightly gripping the shaft at its base Stock seals are supplied as standard with righthand drive springs for clockwise shafts LeftStatic and dynamic Oring seal design differs in a few key ways A static Oring is any oring designed to contact with two or more surfaces that do not move relative to one another, whereas a dynamic Oring is one that helps form a seal between moving partsORing Design Considerations What to Know About ORing Squeeze, Stretch, Compression, and More Our oring groove design guides list default oring groove dimensions for the most basic applications and are intended to be used with the following oring groove design considerations to engineer on oring gland to optimize specific application performance




Duramax Maintenance Free Mechanical Face Seal




Oring Ehandbook
What is the difference between static and dynamic Oring seals?ORing Inside dia (mm 4 digits 1 decimal place)"" O Ring Section (mm 2 digits 1 decimal place) with the decimal point excluded For example is an Oring of 545mm ID with 30 mm section Surface Texture The surface texture of the surfaces in contact with the Oring seals should not exceedCreated Date AM
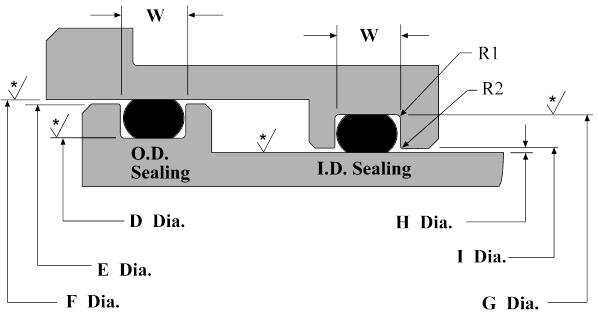



Dynamic O Ring Design Chart Marco Rubber Plastics Custom O Rings Supplier
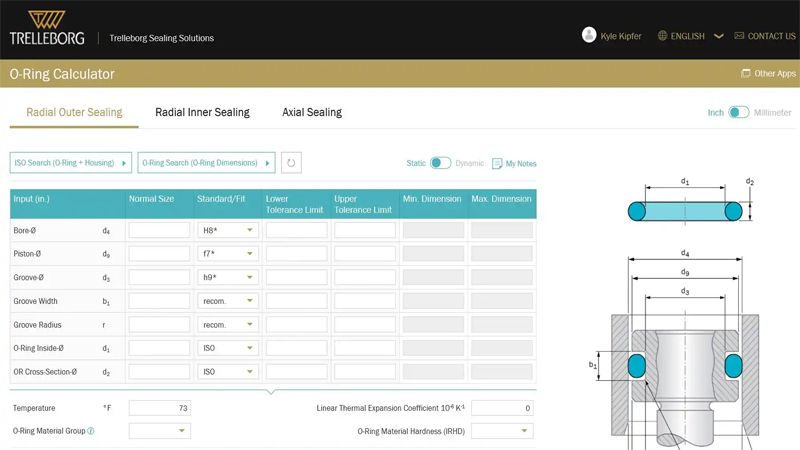



O Ring Calculator Trelleborg Sealing Solutions
Oring seals are typically used for sealing spool valves and for pistons in pneumatic cylinders and similar reciprocating applications Two regimes are possible • With radial compression of the Oring The ring is compressed radially in its groove, with a compression of the crosssection of from 2% to 6%, according to thickness
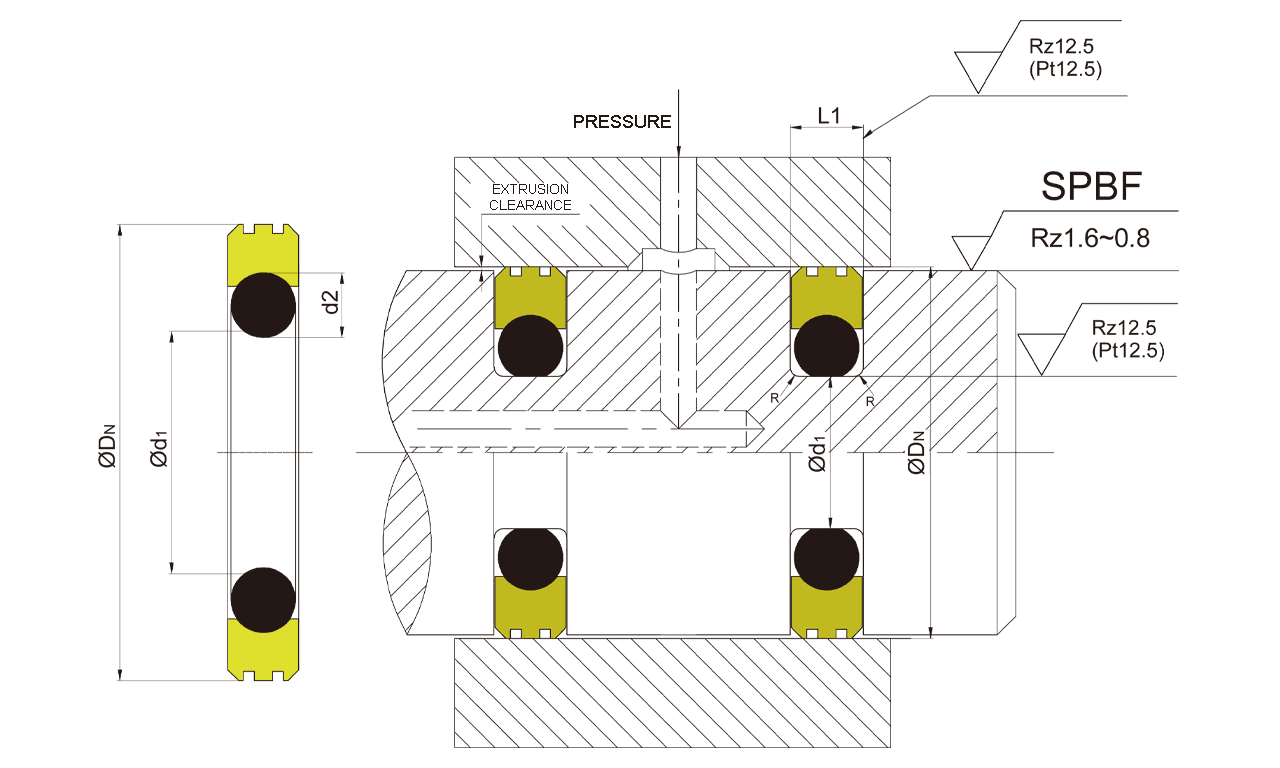



Rotary Seals Design For Construction Machinery Dms Seal Manufacturer




O Ring Groove Design Standard As568b Seal Design Inc




Back Up Rings Anti Extrusion Rings American High Performance Seals
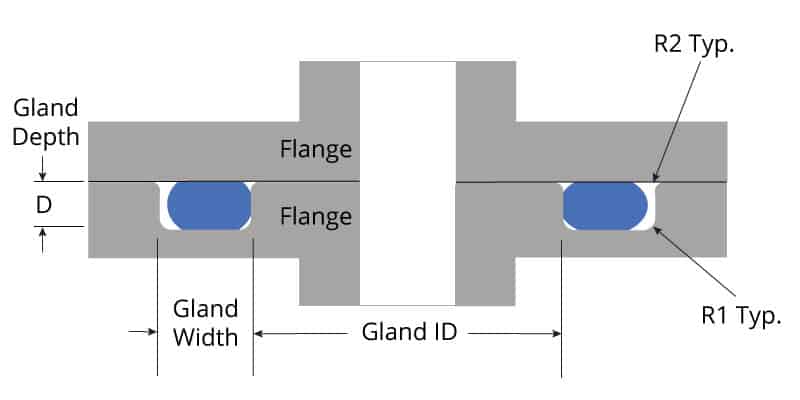



O Ring Groove Design Global O Ring And Seal




Oring Ehandbook



Fundamentals Of Mechanical Seals Seal Faqs
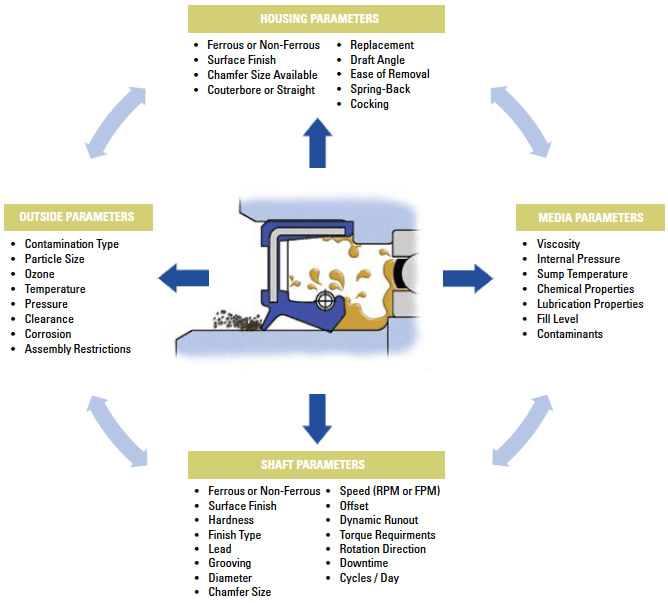



Dynamic Seals Selection Guide Types Features Applications Engineering360



Rotary Shaft Seals




Protech Bearing Isolator Made By Parker The Hope Group Largest Parker Distributor In New England




O Rings O Yeah How To Select Design And Install O Ring Seals Tarkka
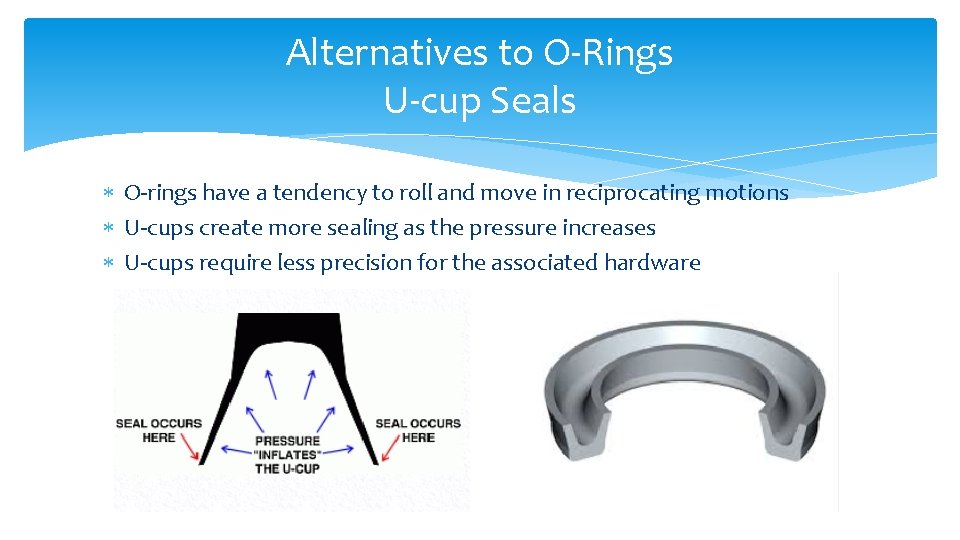



Design Of Oring Seals Design Of Oring Seals
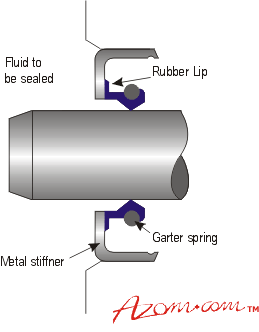



Engineering Seals Seals For Rotating Shafts
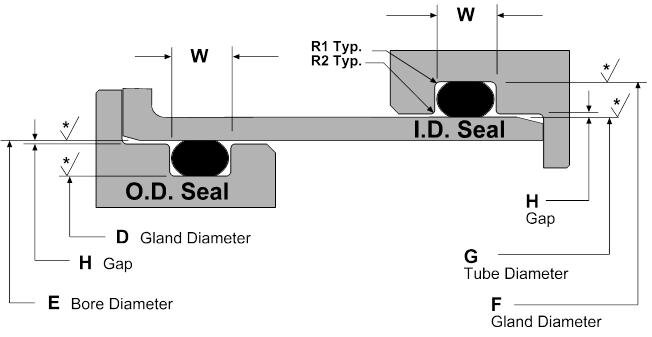



Static O Ring Design Chart Marco Rubber Plastics Custom O Rings Supplier
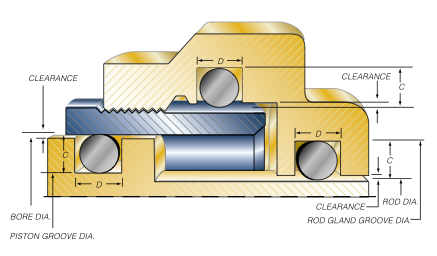



Untitled Document



All Seals Inc The Sealing Specialists
.jpg)



An Introduction To Ptfe Lip Seals For Rotary Applications




Types Of O Ring Applications
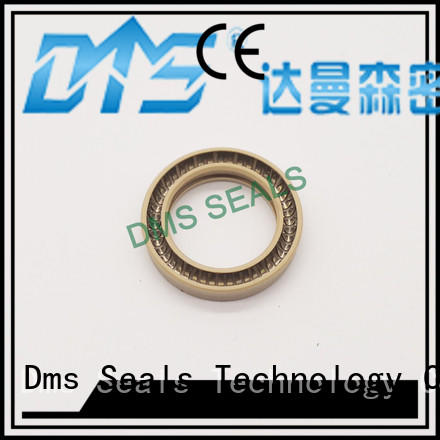



O Ring Shaft Seal Design Dms Seals
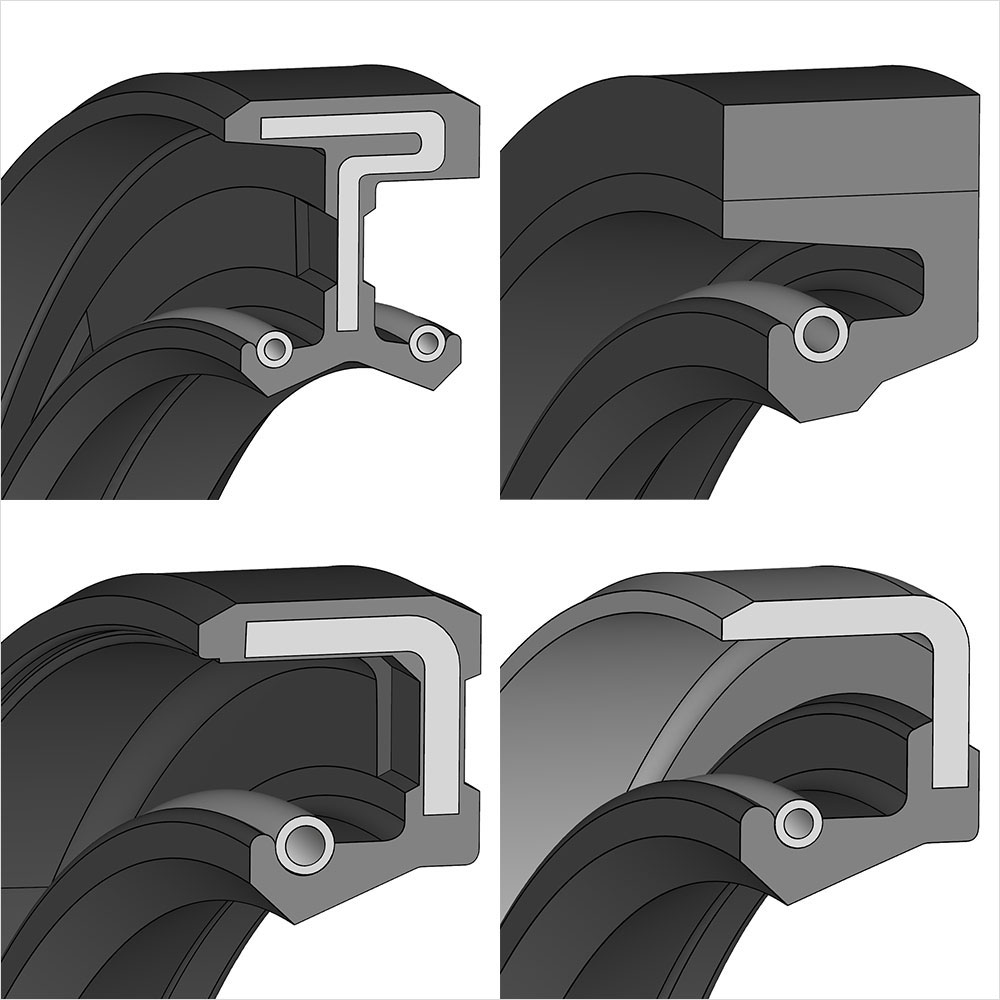



Radial Shaft Seals Freudenberg Fst
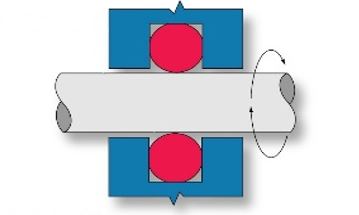



What You Need To Know About Dynamic Seal Applications Hot Topics
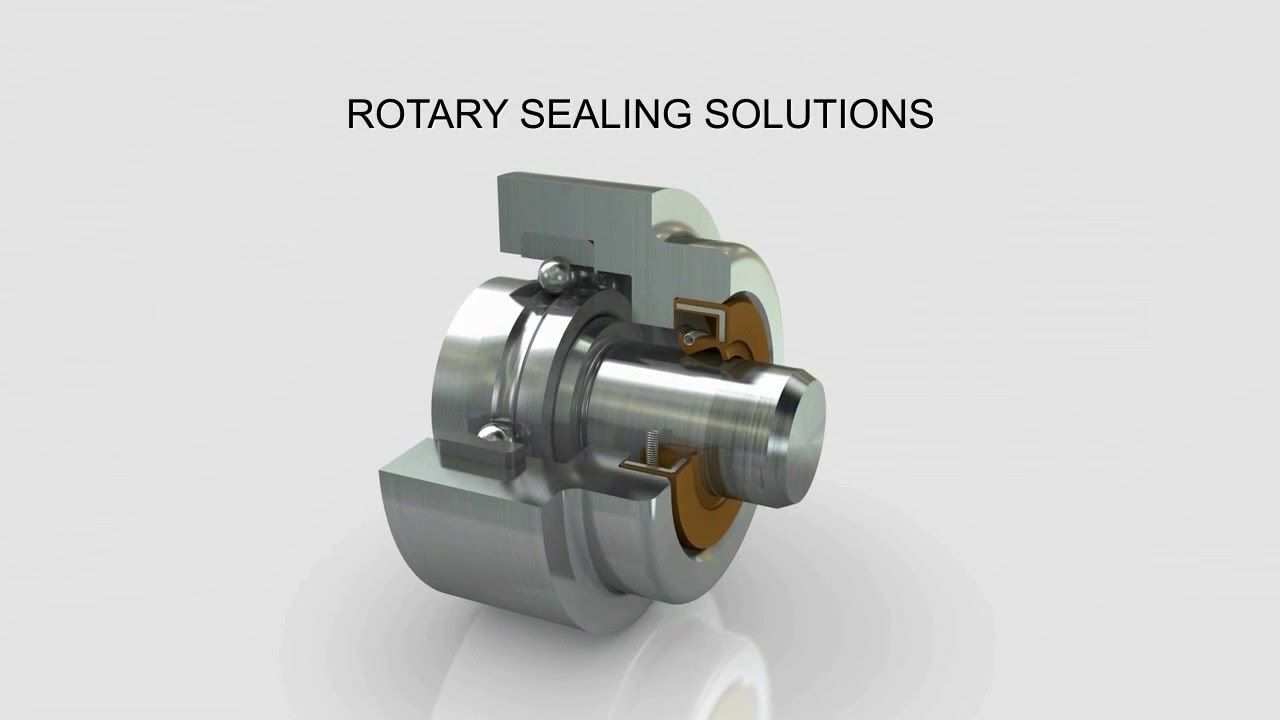



Rotary Sealing Solutions Radial Oil Seals And V Rings Youtube



Untitled Document
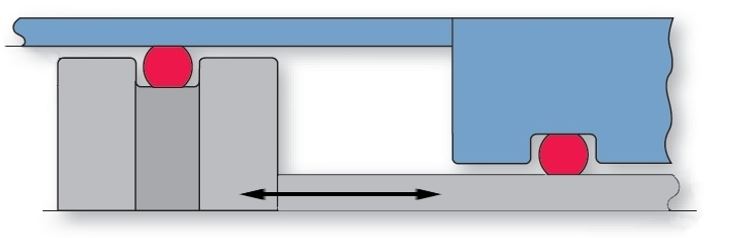



What You Need To Know About Dynamic Seal Applications Hot Topics



Sealink Sealing Mechanism Lubricant Free Mechanical Seal Design Sealink
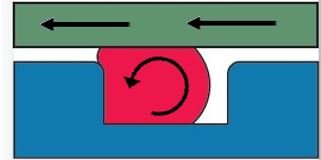



What You Need To Know About Dynamic Seal Applications Hot Topics



2
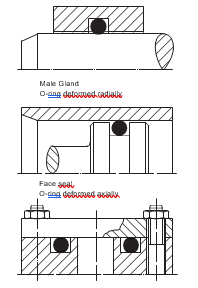



2 Design And Detail Information O Rings Stock O Ring Webshop




Rotary Shaft Seals Seal Design Inc
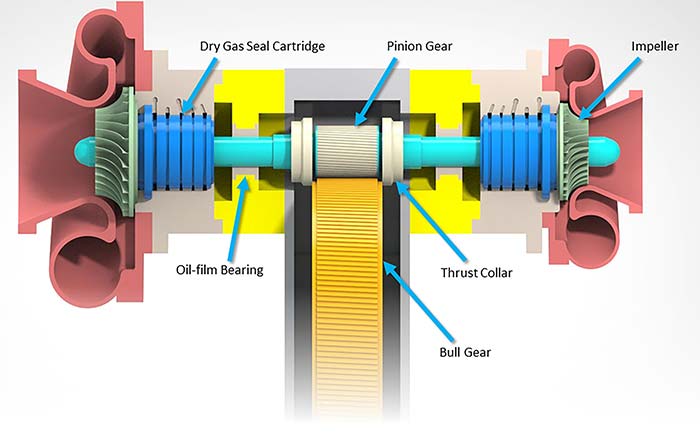



Sealing High Speed Shafts In Turbomachinery Pumps Systems



Dynamic Reciprocating Gland Design Dynamic O Ring Gland




Johncrane Mechanical Seals Type 8 1t With O Ring Seat Rotary Shaft Seal To Replace Johncrane Seals 8 1t Good Quality From China Supplier Manufacturers Made In China Asino Sealing
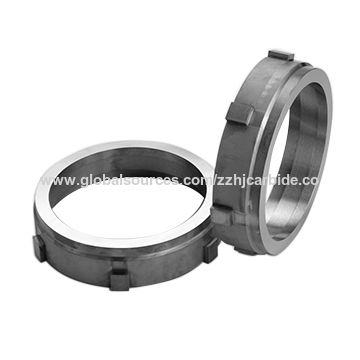



China Accept Custom Design Stellite O Ring Mechanical Shaft Seal Ring On Global Sources Carbide Oem Ring With Holes Finish Machining Mechanical Seal Ring Hard Metal Torus With Holes
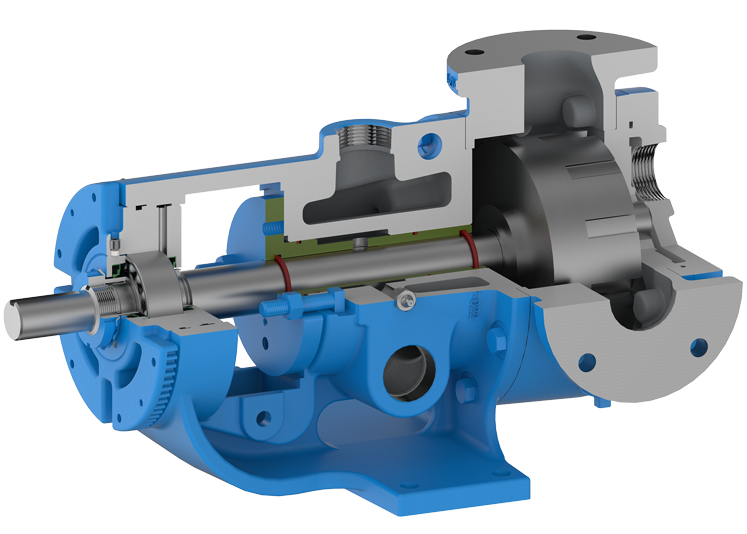



Viking O Pro Barrier Sealing Technology
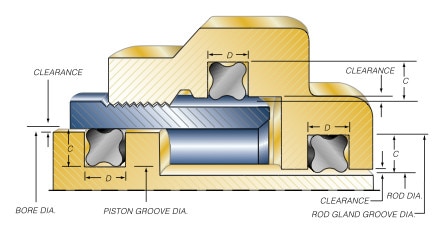



Groove Design Quad Ring Seals Minnesota Rubber Plastics



Dynamic Rotary Gland Design Dynamic O Ring Gland
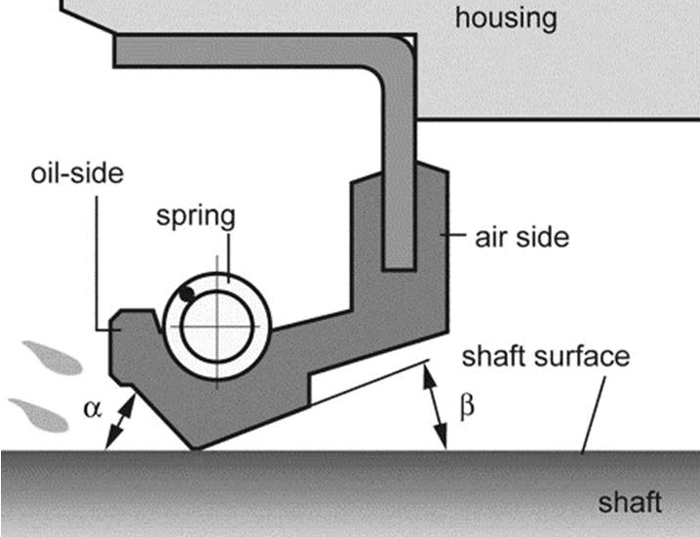



Shaft Seals For Rotating Shafts



Www Pressureseal Com Orings Oguide Pdf




Customized Viton Quad Ring For Dynamic Seal Manufacturers Suppliers Factory Direct Wholesale Xlong




Your Guide To Choosing The Best Rotary Shaft Seal



1




What Is An O Ring Selection Material And Storage Barnwell
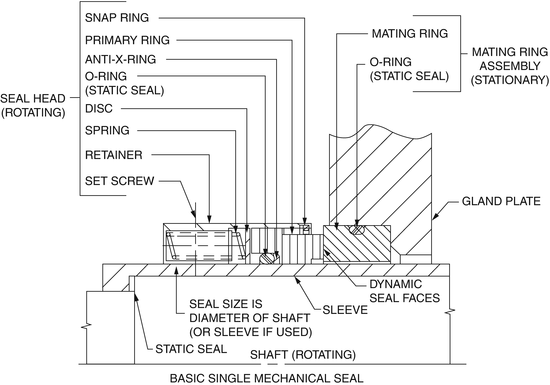



Mechanical Seals Springerlink



Alma Driving Elements Alma Sealing Technology
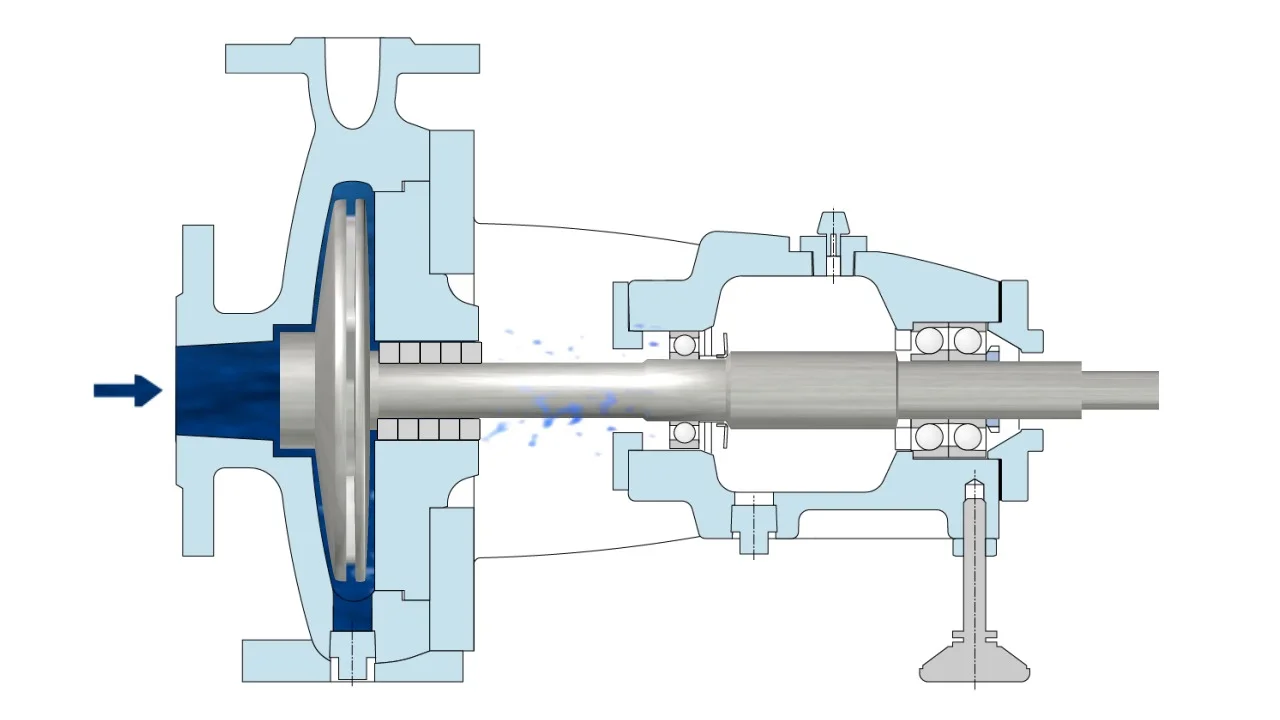



What Is A Mechanical Seal Aesseal




Rotary Sealing With High Pressure Seals Kalsi Engineering
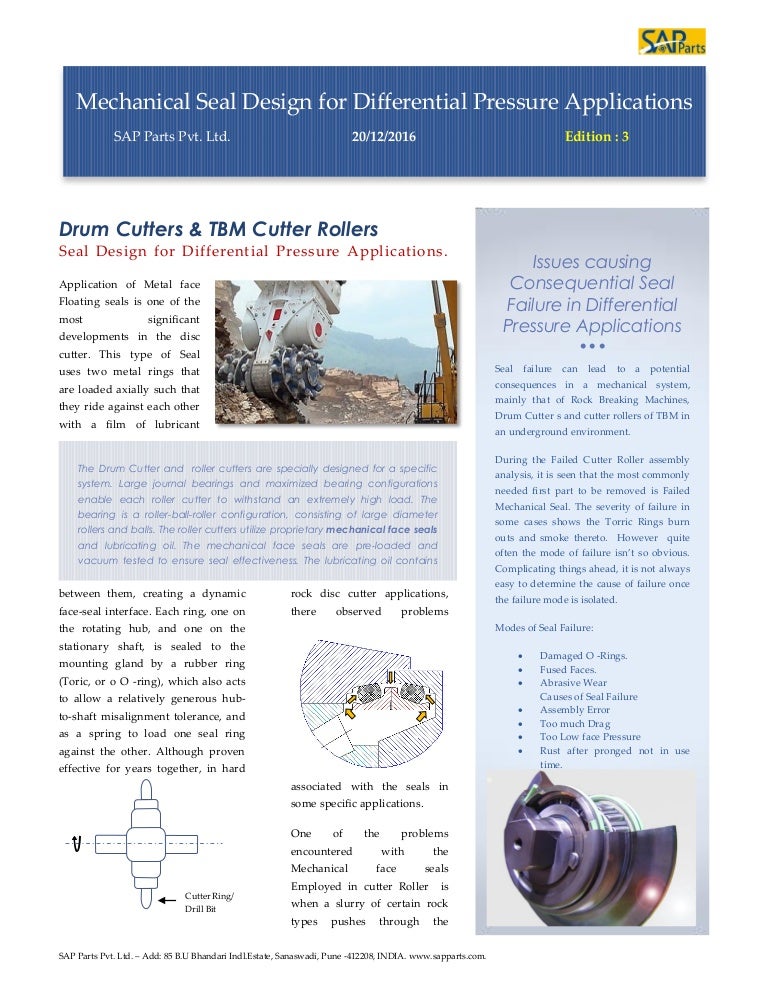



Mechanical Seal Design For Differential Pressure Applications



Http Practicalmaintenance Net Wp Content Uploads Working Design Considerations And Maintenance Of O Rings Pdf




What Are Rotary Shaft Seals Cinchseal




Buna O Ring O Ring In Houston And Minneapolis Dichtomatik
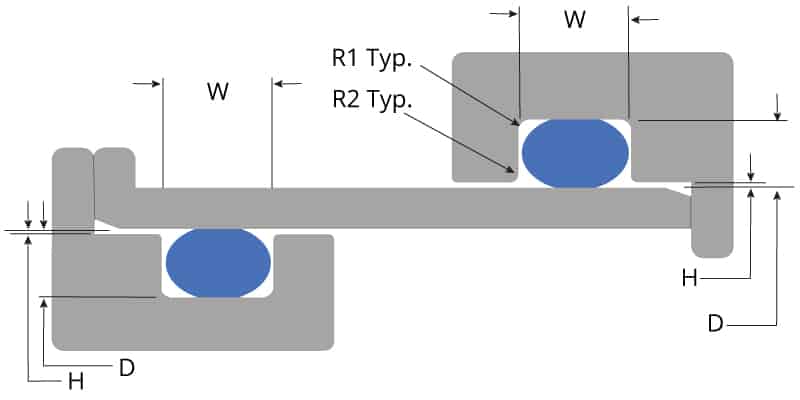



O Ring Groove Design Global O Ring And Seal



Seal Design O Ring Design O Ring Design Guide
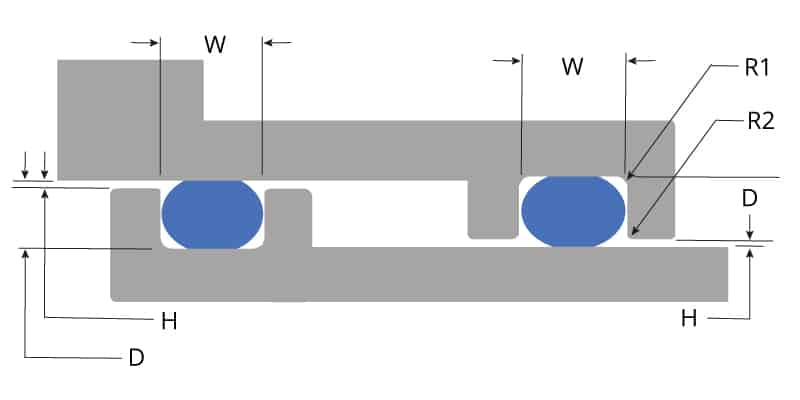



O Ring Groove Design Global O Ring And Seal



Www Hitechseals Com Includes Pdf O Ring Brochure Pdf




O Rings Sealing Australia



1
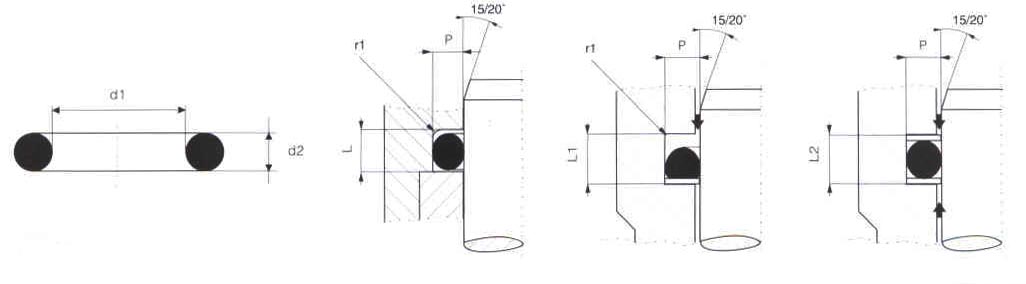



Metric O Ring Groove Design Reference Guide




Lagersmit Lip Seals
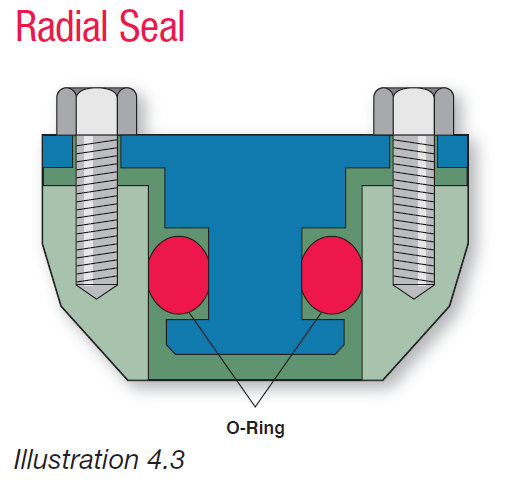



Fundamental Of O Ring
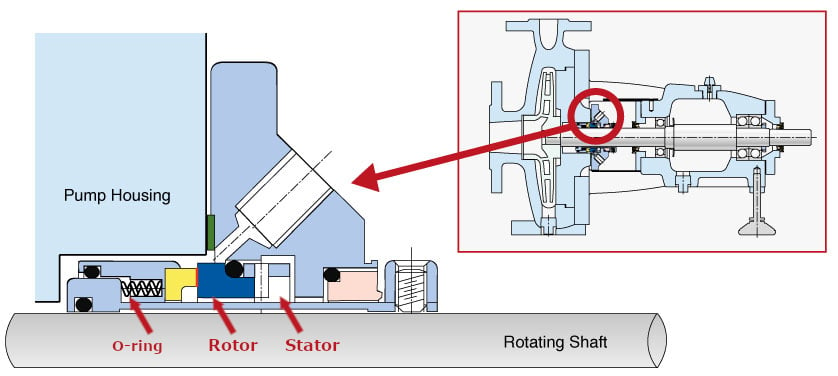



Carbon Graphite Mechanical Seal Types
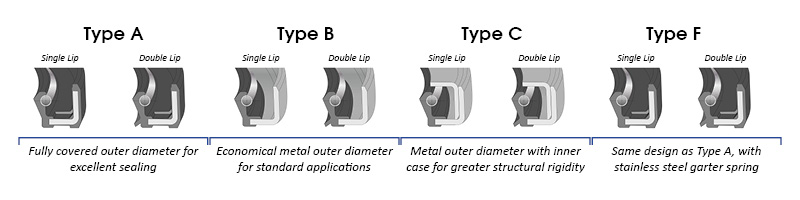



O Rings Archives Polymax Blog



China O Ring Shaft Seal Unbalanced Pusher Type Seal Manufacturers And Suppliers Factory Wholesale Daolin




Mechanical Shaft Seal Types And Sealing Systems Pdf Free Download



Self Centering Seals Design




Seal Solutions Guide




Cartridge Seal An Overview Sciencedirect Topics




Mating Ring An Overview Sciencedirect Topics



Self Centering Seals Design




Shaft Seal Ksb




Duramax Marine Shaft Sealing Systems Drymax Stern Tube Seals
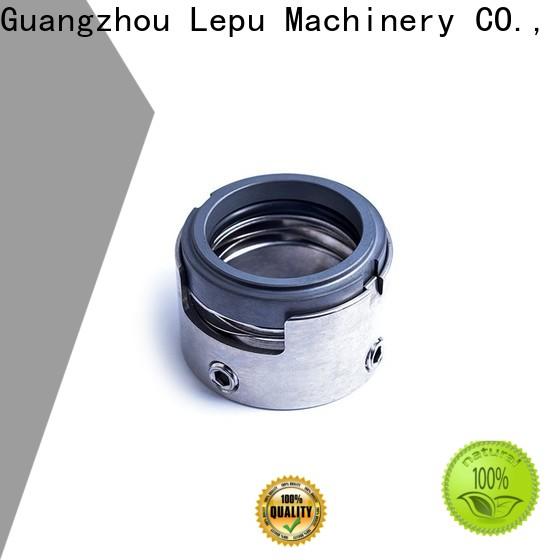



Rotary Shaft Seal Catalog O Ring Lepu
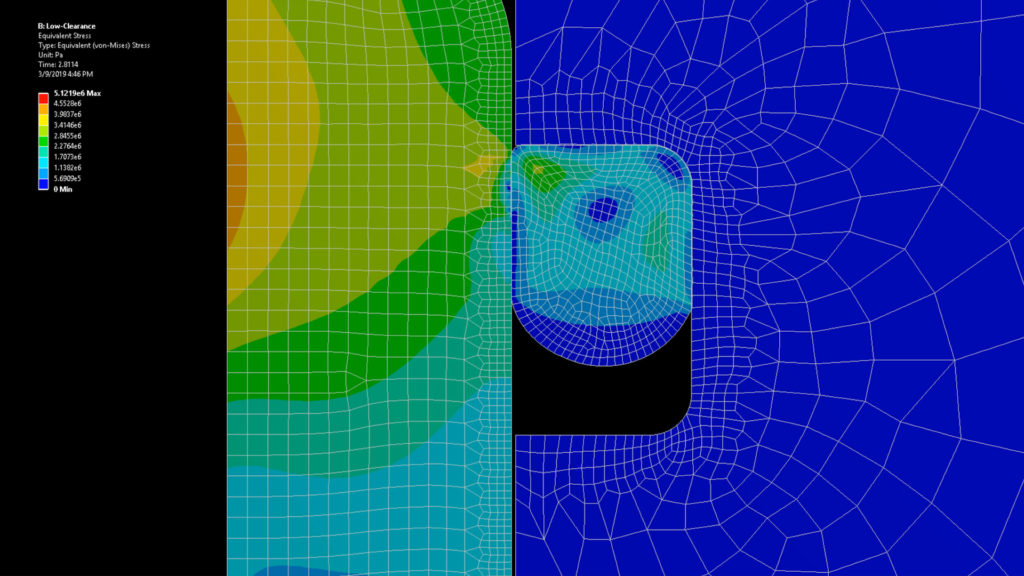



O Rings O Yeah How To Select Design And Install O Ring Seals Tarkka



Http Practicalmaintenance Net Wp Content Uploads Working Design Considerations And Maintenance Of O Rings Pdf
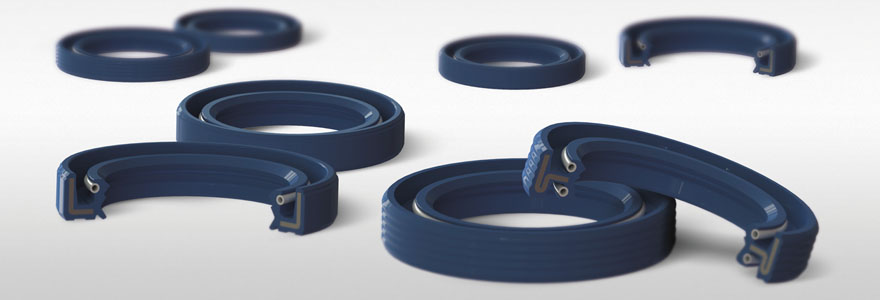



Shaft Seal For Linear Motion Reciprocating Shaft Seal France Joint




Oring Ehandbook




What Is A Mechanical Seal Aesseal
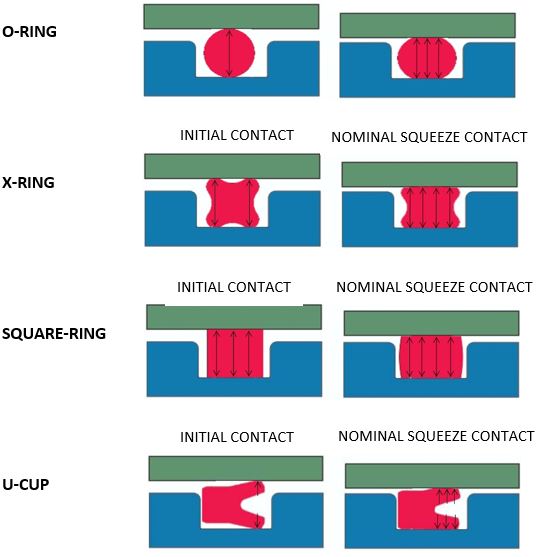



What You Need To Know About Dynamic Seal Applications Hot Topics




O Ring Wikipedia




Johncrane Mechanical Seals Type 8 1t With O Ring Seat Rotary Shaft Seal To Replace Johncrane Seals 8 1t Good Quality From China Supplier Manufacturers Made In China Asino Sealing
0 件のコメント:
コメントを投稿